The global steel industry, which accounts for approximately 7-9% of total global carbon emissions, is at the forefront of the challenge to decarbonize and contribute to achieving “net zero” goals. As one of the most energy-intensive industries, its transformation is pivotal in combating climate change. Central to this transformation is the role of Electric Arc Furnaces (EAFs), which offer a more sustainable method of steel production compared to traditional blast furnaces. As nations and corporations commit to carbon neutrality, the steel industry, driven by the adoption of EAF technology, is poised to play a key role in the net-zero transition.
The Promise of Electric Arc Furnaces: A Greener Approach
EAFs represent a more environmentally friendly approach to steelmaking. Unlike traditional blast furnaces, which use iron ore and coke (a derivative of coal) as primary inputs, EAFs primarily recycle scrap steel, using electricity to melt it down into reusable material. This method dramatically reduces the need for raw materials and energy consumption. The process itself generates fewer direct carbon emissions compared to the blast furnace method, which relies heavily on coal and emits large quantities of carbon dioxide.
- Reduction in CO2 emissions: On average, EAFs emit around 0.4 tons of CO2 per ton of steel produced, compared to the 2.2 tons emitted by blast furnaces. This significant reduction positions EAFs as an ideal solution for lowering the carbon footprint of the steel industry.
- Recycling of steel scrap: EAFs’ reliance on scrap material reduces the demand for virgin iron ore, leading to less mining and environmental degradation. Recycling steel also saves considerable energy — approximately 75% less than producing iron ore steel.
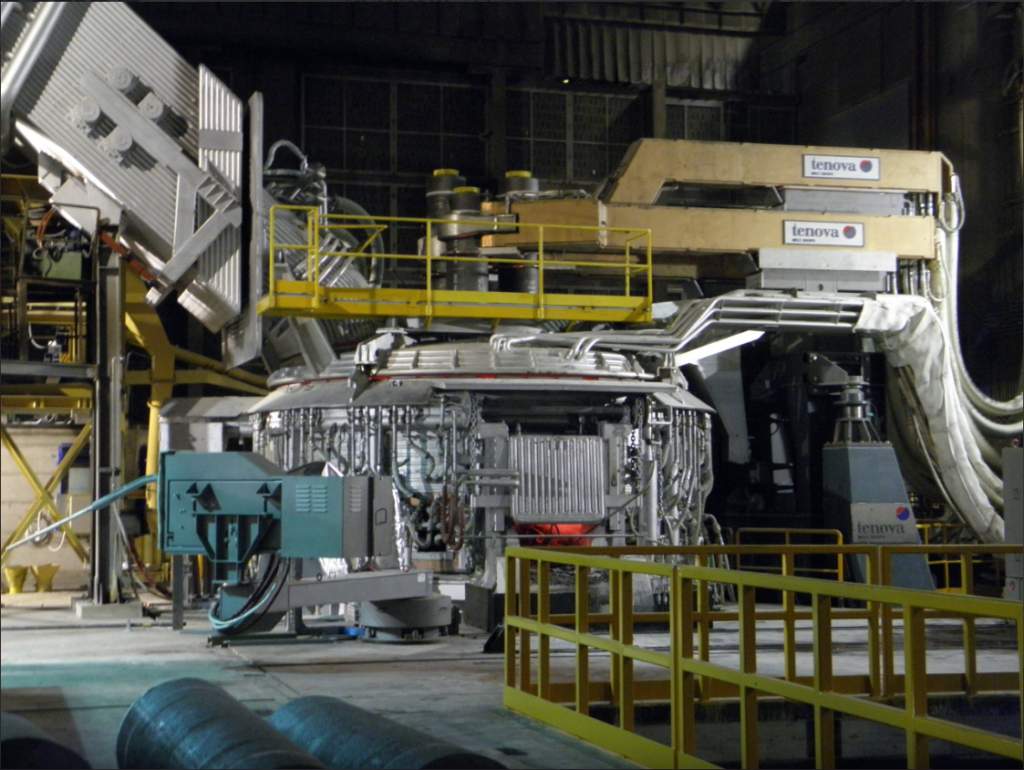
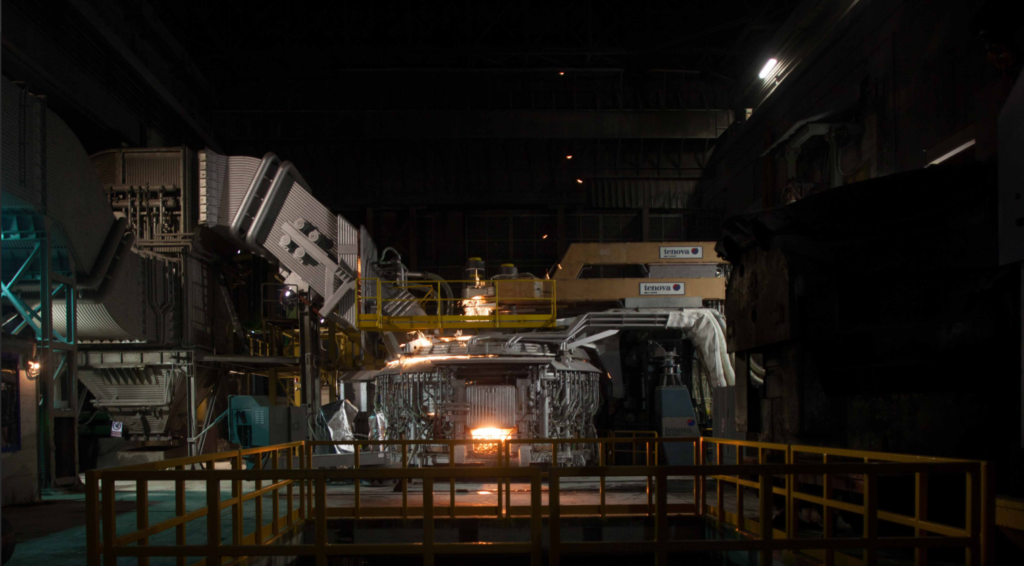
image from Tenova
Enhancing the Sustainability of EAFs: Green Energy Integration
While EAFs are a step toward decarbonization, their potential impact on the net-zero goals is amplified when integrated with renewable energy. Currently, EAFs require a substantial amount of electricity to melt steel scrap, and in many regions, the electricity grid is still powered by fossil fuels, which offsets some of the environmental benefits of EAFs. For EAFs to truly contribute to net-zero emissions, the electricity used must be derived from clean, renewable sources such as wind, solar, or hydropower.
- Decarbonizing electricity grids: Governments and industries must prioritize decarbonizing electricity grids. A fully decarbonized energy supply for EAFs would result in near-zero emissions for this method of steelmaking.
- Hydrogen-powered EAFs: Looking beyond renewable electricity, there is also the potential for hydrogen-powered EAFs. Hydrogen, if produced from renewable sources, can serve as a clean fuel for heating in the steel production process, further reducing dependency on fossil fuels and lowering emissions.
The Growing Adoption of EAFs: A Global Perspective
Several countries and steel producers have recognized the environmental benefits of EAFs and have begun incorporating them into their operations. Europe, in particular, has taken the lead, with nations such as Sweden and Germany setting ambitious targets to decarbonize their steel industries. In the United States, where scrap steel is abundant, the share of EAF-produced steel already surpasses 70%. Developing nations are also looking to adopt EAF technology, though the availability of scrap steel remains a limiting factor in some regions.
- Sweden’s HYBRIT project: The groundbreaking HYBRIT project in Sweden aims to produce fossil-free steel by replacing coal in traditional steelmaking with hydrogen, combining the use of both EAFs and direct reduction technology. Such projects are indicative of the industry’s long-term strategy to pivot toward greener steel production.
- China’s EAF transformation: China, the largest steel producer in the world, has begun shifting its focus toward EAFs as part of its carbon reduction strategy. Currently, EAFs account for about 15% of China’s steel production, but this is expected to increase as the country moves away from coal-intensive blast furnaces in response to its net-zero pledge.
Overcoming Challenges: Availability of Scrap and Technological Advancements
Despite the advantages, the widespread adoption of EAFs faces certain challenges. The availability of scrap steel is a critical limiting factor, especially in countries with less industrial recycling infrastructure. Additionally, the quality of steel produced through EAFs can be lower when using scrap containing impurities, although advances in sorting and refining technology are helping to address these issues.
- Scrap availability: The global steel industry must ensure a steady supply of quality scrap steel for EAFs. This requires better recycling infrastructure and the development of scrap trading markets in regions where it is currently limited.
- Technological innovations: Continued innovation in refining techniques will be essential to improve the quality of steel from EAFs, particularly for high-grade steel used in automotive and construction industries. Investments in advanced sensors, machine learning for scrap sorting, and purification methods will be key to overcoming these challenges.
EAFs in the Net-Zero Context: A Path Forward
To achieve net-zero emissions by 2050, the steel industry must rapidly transition away from traditional coal-based blast furnaces. EAFs, with their ability to produce steel using recycled materials and renewable energy, present a viable pathway for reducing the sector’s carbon footprint. However, the full potential of EAFs can only be realized with complementary actions such as decarbonizing the electricity grid, enhancing recycling systems, and advancing the technological capabilities of steel production.
The journey to net zero in the steel industry is not without its obstacles, but the adoption of Electric Arc Furnaces will be a decisive factor in the industry’s ability to meet global climate goals. As governments, industries, and consumers increasingly prioritize sustainability, the role of EAFs will only continue to grow, marking a crucial shift toward a greener and more sustainable steel industry.